詳細なPCBA製造プロセス(DIPの全プロセスを含む)をぜひご覧ください。
「ウェーブはんだ付けプロセス」
ウェーブはんだ付けは、通常、プラグイン デバイスの溶接プロセスです。これは、溶融した液体はんだがポンプの助けを借りて、はんだタンクの液面上に特定の形状のはんだ波を形成し、挿入された部品の PCB が特定の位置ではんだ波のピークを通過するプロセスです。下図に示すように、はんだ接合部の溶接を実現するための伝動チェーンの角度と一定の浸漬深さ。
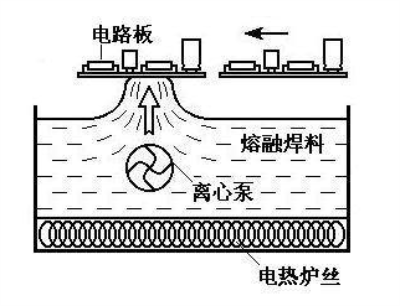
一般的なプロセス フローは次のとおりです。下図に示すように、デバイスの挿入 -- PCB のロード -- ウェーブはんだ付け -- PCB のアンロード -- DIP ピンのトリミング -- 洗浄です。
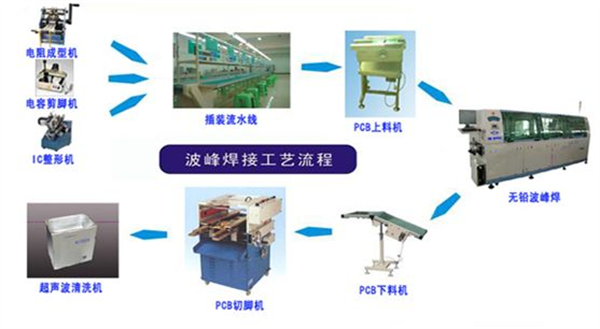
1.THC挿入技術
1. 部品ピンの形成
DIP デバイスは挿入前に形状を整える必要があります
(1)手作業による部品整形:曲がったピンは、下図のようにピンセットや小型ドライバーを使って整形できます。
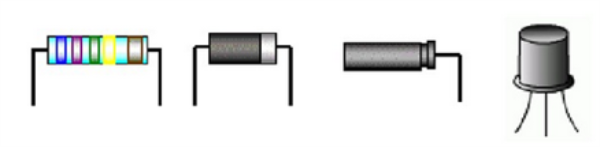
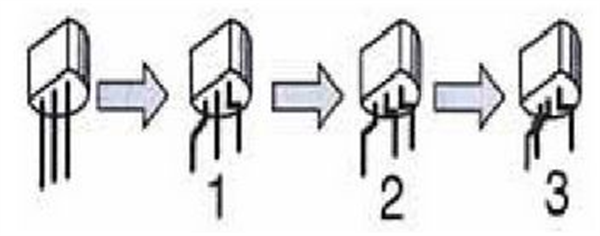
(2) 部品成形の機械加工: 部品の機械成形は特殊な成形機械で完了します。その動作原理は、フィーダーが振動送りを使用して材料 (プラグイン トランジスタなど) を供給することです。トランジスタの場合、最初のステップは、左側と右側の両側のピンを曲げることです。 2 番目のステップでは、中央のピンを前後に曲げて成形します。次の図に示すように。
2. コンポーネントを挿入する
スルーホール挿入技術は手動挿入と自動機械挿入に分けられます
(1) 手動挿入および溶接の場合は、まずパワーデバイスの冷却ラック、ブラケット、クリップなど、機械的に固定する必要があるコンポーネントを挿入し、次に溶接して固定する必要があるコンポーネントを挿入します。挿入時は部品ピンや印刷版の銅箔に直接触れないようにしてください。
(2) 機械的自動プラグイン (AI と呼ばれる) は、現代の電子製品の設置における最も先進的な自動生産技術です。自動機械装置の設置では、最初に高さの低いコンポーネントを挿入し、次に高さの高いコンポーネントを設置する必要があります。貴重な主要コンポーネントは最終インストールに組み込む必要があります。放熱ラック、ブラケット、クリップなどの取り付けは溶接プロセスに近い必要があります。 PCB コンポーネントの組み立て順序を次の図に示します。
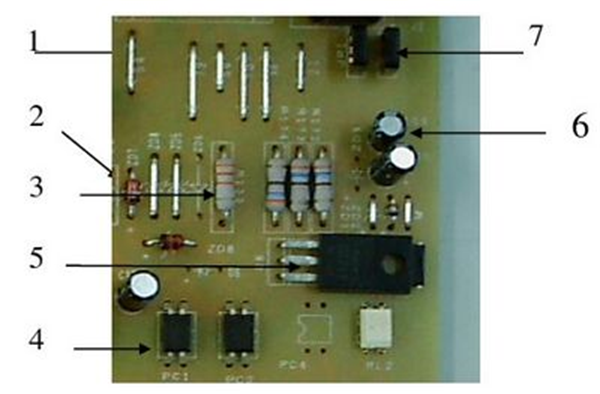
3. ウェーブはんだ付け
(1) ウェーブソルダリングの動作原理
ウェーブはんだ付けは、ポンプの圧力によって溶融したはんだの表面に特定の形状のはんだの波を形成し、部品とともに挿入されたアセンブリ部品がはんだを通過するときにピン溶接領域にはんだスポットを形成する技術の一種です。一定の角度で波を打ちます。コンポーネントは、チェーンコンベアによる搬送プロセス中に溶接機の予熱ゾーンで最初に予熱されます (コンポーネントの予熱と到達温度は、所定の温度曲線によって制御されます)。実際の溶接では、通常、部品表面の予熱温度を制御する必要があるため、多くの装置に対応する温度検出装置 (赤外線検出器など) が追加されています。予熱後、アセンブリをリード溝に入れて溶接します。ブリキのタンクには溶融した液体はんだが入っており、スチールタンクの底にあるノズルが溶融はんだの一定形状の波頭をスプレーするため、部品の溶接面が波を通過するときに、はんだの波によって加熱されます。 、はんだ波も溶接領域を湿らせて膨張して充填し、最終的に溶接プロセスが完了します。その動作原理を下の図に示します。
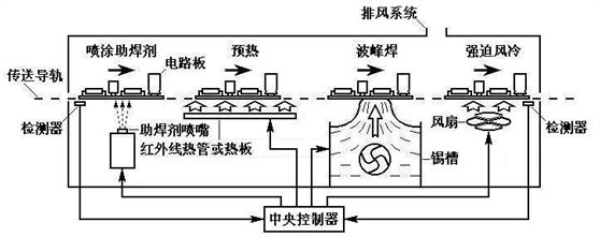
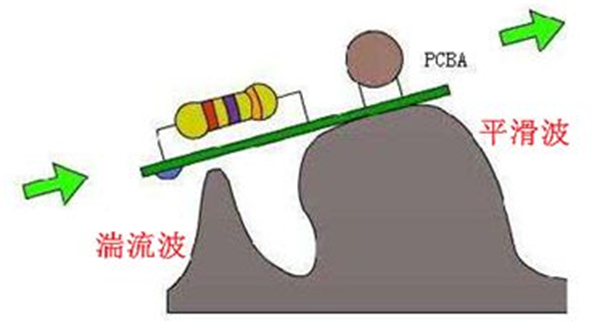
ウェーブはんだ付けでは、対流熱伝達原理を利用して溶接領域を加熱します。溶融はんだ波は熱源として働き、ピン溶接部を洗浄するために流れる一方で、熱伝導の役割も果たし、この作用によりピン溶接部が加熱される。溶接領域を確実に加熱するために、通常はんだウェーブは一定の幅を持っており、コンポーネントの溶接面がウェーブを通過するときに十分な加熱や濡れなどが行われます。従来のウェーブはんだ付けでは、一般に単一ウェーブが使用され、ウェーブは比較的平坦です。鉛はんだの使用により、現在はダブルウェーブの形で採用されています。次の図に示すように。
コンポーネントのピンは、半田が固体状態で金属化されたスルーホールに浸漬するための手段を提供します。ピンがはんだ波に接触すると、液体はんだが表面張力によってピンと穴の壁を登ります。メタライズされたスルーホールの毛細管現象により、はんだの登りが改善されます。はんだは PcB パッドに到達すると、パッドの表面張力の作用により広がります。上昇するはんだはフラックスガスと空気をスルーホールから排出し、これによりスルーホールが充填され、冷却後にはんだ接合部が形成されます。
(2) ウェーブ溶接機の主要構成部品
ウェーブ溶接機は主に、ベルトコンベア、ヒーター、ブリキタンク、ポンプ、フラックス発泡(またはスプレー)装置で構成されています。下図に示すように、主にフラックス添加ゾーン、予熱ゾーン、溶接ゾーン、冷却ゾーンに分かれています。
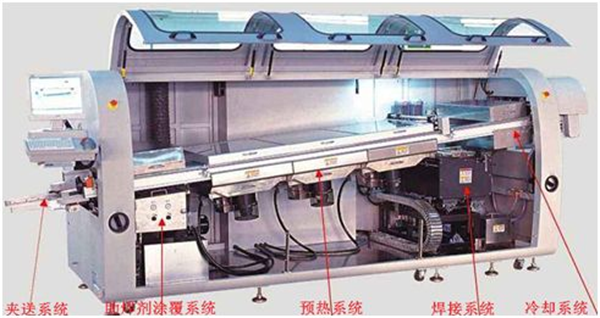
3. ウェーブソルダリングとリフロー溶接の主な違い
ウェーブソルダリングとリフロー溶接の主な違いは、溶接時の加熱源とはんだ供給方法が異なることです。ウェーブはんだ付けでは、タンク内ではんだを予熱して溶かし、ポンプから発生するはんだウェーブが熱源とはんだ供給の2つの役割を果たします。溶融はんだ波は、PCB のスルーホール、パッド、コンポーネント ピンを加熱すると同時に、はんだ接合部の形成に必要なはんだも提供します。リフローはんだ付けでは、基板の溶接箇所にはんだ(はんだペースト)があらかじめ塗布されており、リフロー時の熱源ははんだを再溶融する役割を果たします。
(1) 3 選択ウェーブはんだ付けプロセスの概要
ウェーブはんだ付け装置は50年以上前に発明され、スルーホール部品や回路基板の製造において生産効率が高く、生産量が多いという利点があり、かつては半田付けの自動量産において最も重要な溶接装置でした。電子製品。ただし、その適用にはいくつかの制限があります。(1) 溶接パラメータが異なります。
同じ回路基板上の異なるはんだ接合では、その特性 (熱容量、ピンの間隔、錫の浸透要件など) が異なるため、非常に異なる溶接パラメータが必要になる場合があります。ただし、ウェーブはんだ付けの特徴は、同じ設定パラメータの下で回路基板全体のすべてのはんだ接合部の溶接を完了することであるため、異なるはんだ接合部が互いに「落ち着く」必要があるため、ウェーブはんだ付けが溶接を完全に満たすことがより困難になります。高品質の回路基板の要件。
(2) 高い運用コスト。
従来のウェーブはんだ付けの実用化では、プレート全体にフラックスをスプレーし、錫スラグが発生するため、操業コストが高くなります。特に鉛フリー溶接の場合、鉛フリーはんだの価格は鉛はんだの3倍以上であるため、スズスラグによる操業コストの増加は非常に驚くべきものです。さらに、鉛フリーはんだはパッド上の銅を溶かし続け、錫シリンダー内のはんだの組成は時間の経過とともに変化します。これを解決するには、純錫と高価な銀を定期的に追加する必要があります。
(3)メンテナンスやメンテナンスのトラブル。
製造中の残留フラックスはウェーブはんだ付けの伝達システムに残り、生成されたスズスラグを定期的に除去する必要があるため、ユーザーはより複雑な装置のメンテナンスとメンテナンス作業を必要とします。このような理由から、選択的ウェーブはんだ付けが登場しました。
いわゆる PCBA 選択ウェーブはんだ付けでは、依然としてオリジナルの錫炉が使用されていますが、違いは、以下の図に示すように、基板を錫炉キャリアに配置する必要があることです。これは、炉の治具についてよく言われることです。
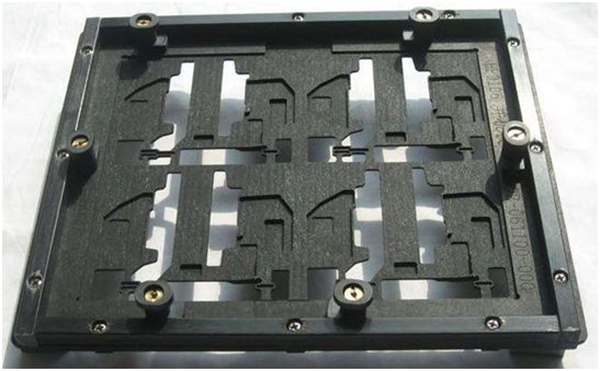
以下に示すように、ウェーブはんだ付けが必要な部品は錫に露出され、他の部品は車両の被覆で保護されます。これは、プールに救命浮輪を取り付けるのと似ています。救命浮輪で覆われた場所には水が入りませんが、ブリキのストーブに置き換えると、車両で覆われている場所には当然ブリキが入りません。錫の再溶解や部品の落下の問題はありません。
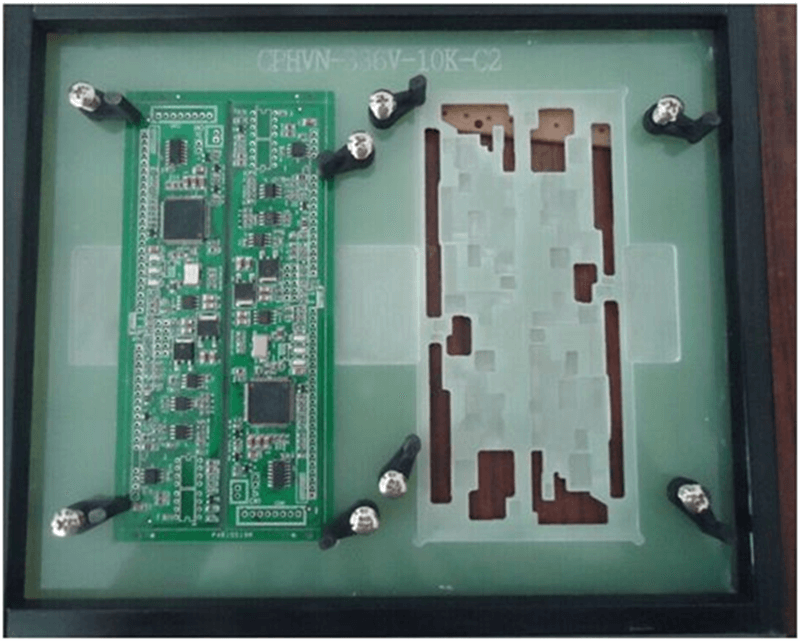
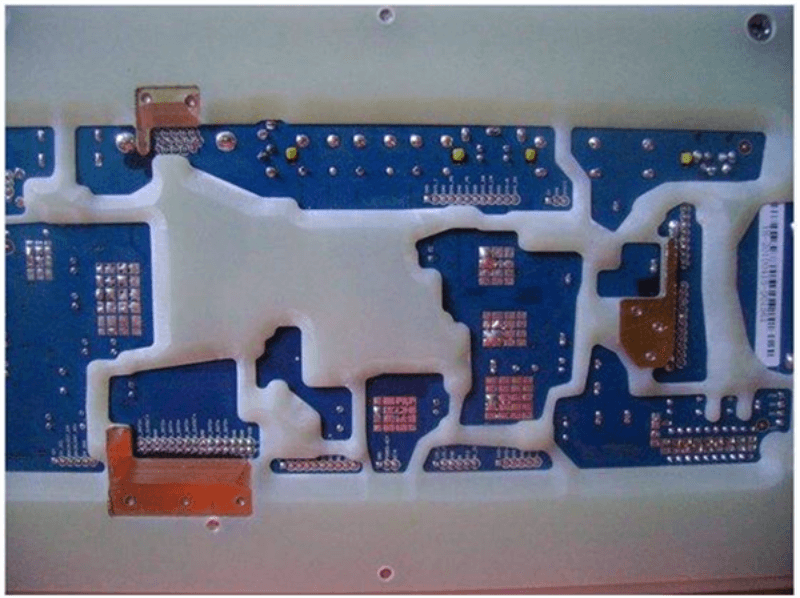
「スルーホールリフロー溶接工程」
スルーホールリフロー溶接は、コンポーネントを挿入するためのリフロー溶接プロセスであり、主にいくつかのプラグインを含む表面アセンブリプレートの製造に使用されます。その技術の核となるのがソルダペーストの塗布方法です。
1. プロセスの紹介
スルーホールリフロー溶接は、はんだペーストの塗布方法により、パイプ印刷スルーホールリフロー溶接法、はんだペースト印刷スルーホールリフロー溶接法、成形ブリキ板スルーホールリフロー溶接法の3種類に分けられます。
1) チューブラー印刷スルーホールリフロー溶接プロセス
管状印刷スルーホールリフロー溶接プロセスは、スルーホール部品リフロー溶接プロセスの最も初期の応用であり、主にカラー TV チューナーの製造に使用されます。プロセスの中核となるのは、はんだペースト管状プレスです。そのプロセスは次の図に示されています。
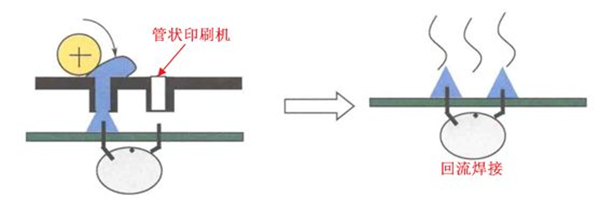
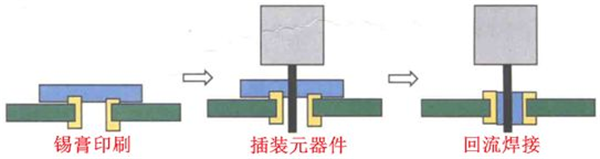
2) はんだペースト印刷スルーホールリフロー溶接工程
はんだペースト印刷スルーホールリフロー溶接プロセスは、現在最も広く使用されているスルーホールリフロー溶接プロセスであり、主に少数のプラグインを含む混合PCBAに使用されます。プロセスは従来のリフロー溶接プロセスと完全に互換性があり、特別なプロセス装置は必要ありません。唯一の要件は、溶接されたプラグイン コンポーネントがスルー ホール リフロー溶接に適していることです。そのプロセスを次の図に示します。
3) 成形ブリキ板スルーホールリフロー溶接工程
成形錫シートのスルーホールリフロー溶接プロセスは、主に多ピンコネクタに使用されます。はんだははんだペーストではなく成形錫シートで、通常はコネクタメーカーが直接追加し、アセンブリは加熱するだけです。
スルーホールリフロー設計要件
1.PCB設計要件
(1) PCB 厚さ 1.6 mm 以下の基板に適しています。
(2) パッドの最小幅は 0.25 mm で、溶融したはんだペーストは 1 回「引っ張られ」、錫ビードは形成されません。
(3) コンポーネントの基板外ギャップ (スタンドオフ) は 0.3mm より大きい必要があります。
(4) パッドから出るリードの長さは0.25~0.75mmが適当です。
(5) 0603 などのファインスペース部品とパッド間の最小距離は 2mm です。
(6) スチールメッシュの最大目開きは1.5mm拡大可能です。
(7)口径はリード径に0.1~0.2mmを加えた寸法となります。次の図に示すように。
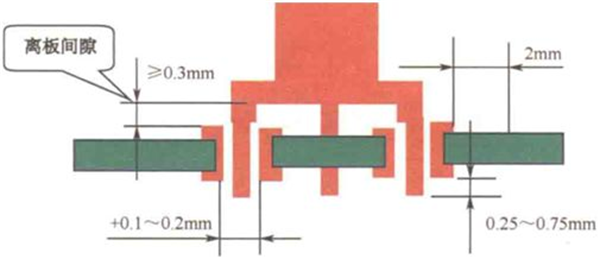
「スチールメッシュ窓開口要件」
一般に、50%の穴充填を達成するには、スチールメッシュウィンドウを拡張する必要があります。外部拡張の具体的な量は、PCBの厚さ、スチールメッシュの厚さ、穴とリードの間のギャップに従って決定する必要があります。およびその他の要因。
一般に、膨張が 2mm を超えない限り、はんだペーストは引き戻され、穴に充填されます。次の図に示すように、外部拡張はコンポーネント パッケージによって圧縮できないか、コンポーネントのパッケージ本体を避けて片面に錫ビーズを形成する必要があることに注意してください。
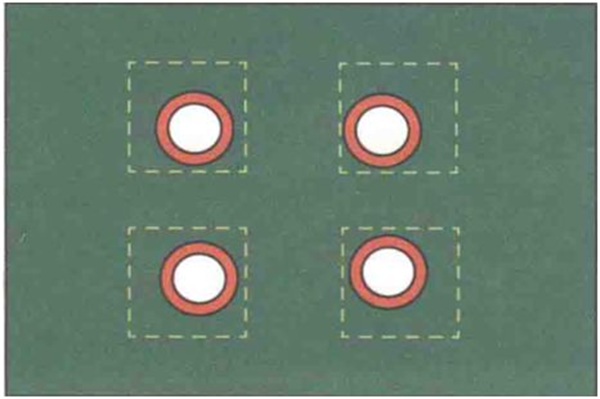
「従来のPCBA組立工程のご紹介」
1) 片面実装
処理の流れを以下の図に示します
2) 片面挿入
プロセス フローを以下の図 5 に示します。
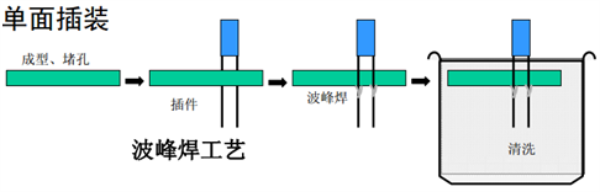
ウェーブはんだ付けによるデバイス ピンの形成は、生産プロセスの中で最も効率の悪い部分の 1 つであり、それに応じて静電気損傷のリスクが生じ、納期が長くなり、エラーの可能性も高まります。
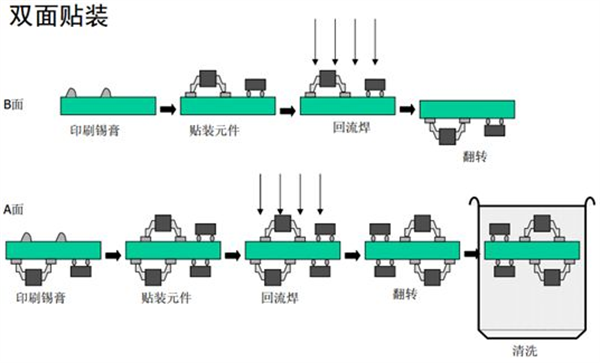
3) 両面実装
処理の流れを以下の図に示します
4) 片面混合
処理の流れを以下の図に示します
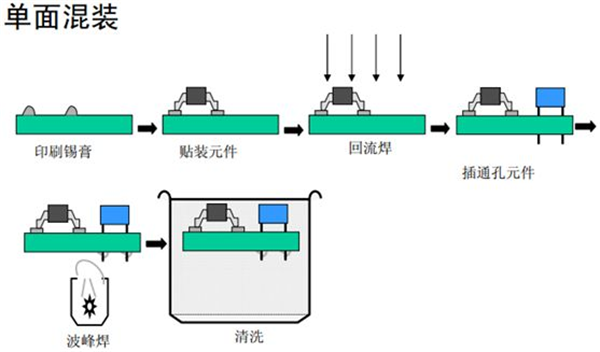
スルーホール部品が少ない場合は、リフロー溶接や手溶接が可能です。
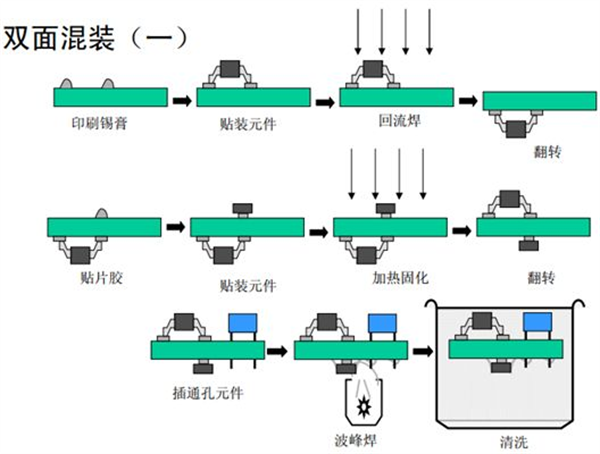
5) 両面混合
処理の流れを以下の図に示します
両面 SMD デバイスが多く、THT コンポーネントが少ない場合は、プラグイン デバイスをリフローまたは手動溶接できます。処理フローを以下に示します。
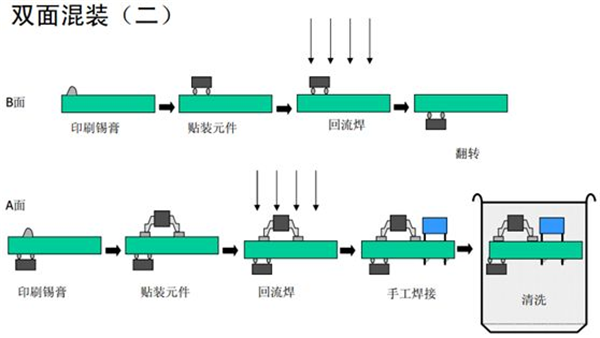