SMT は従来のソルダ ペースト エア リフロー溶接キャビティの解析とソリューション (2023 Essence Edition) を使用しています。その価値はあります。
1 はじめに

回路基板アセンブリでは、まず回路基板のはんだパッド上にはんだペーストが印刷され、その後、さまざまな電子部品が固定されます。最後に、リフロー炉の後、はんだペースト内の錫ビーズが溶解し、あらゆる種類の電子部品と回路基板のはんだパッドが溶接されて、電気サブモジュールが組み立てられます。表面実装技術 (sMT) は、システム レベル パッケージ (siP)、ボールグリッド アレイ (BGA) デバイス、パワー ベア チップ、スクエア フラット ピンレス パッケージ (クワッド aatノーリード、QFN と呼ばれる) などの高密度パッケージング製品での使用が増加しています。 ) デバイス。
はんだペーストの溶接プロセスと材料の特性により、これらの大きなはんだ表面デバイスのリフロー溶接後、はんだ溶接領域に穴ができ、製品の電気的特性、熱的特性、機械的特性に影響を与えます。はんだペーストのリフロー溶接キャビティを改善することは、解決しなければならないプロセスおよび技術的問題となっており、一部の研究者はBGAのはんだボール溶接キャビティの原因を分析および研究し、改善ソリューションを提供しています。ペーストリフロー溶接プロセス QFN の溶接面積が 10mm2 を超える、または溶接面積が 6mm2 を超えるベアチップのソリューションが不足しています。
溶接穴の改善にはプリフォーム半田溶接や真空還流炉溶接をご利用ください。既製はんだには、フラックスを点着するための特別な装置が必要です。たとえば、チップを既製のはんだ上に直接配置した後、チップはオフセットされ、大きく傾いてしまいます。フラックス マウント チップをリフローしてからポイントする場合、プロセスはリフロー 2 回分増加し、既製のはんだとフラックス材料のコストははんだペーストよりもはるかに高くなります。
真空還流装置はより高価であり、独立した真空チャンバーの真空能力は非常に低く、コストパフォーマンスは高くありません。また、錫飛散の問題は深刻であり、これは高密度および狭ピッチのアプリケーションで重要な要素です。製品。本稿では、従来のはんだペーストリフロー溶接プロセスに基づいて、溶接キャビティを改善し、溶接キャビティによって引き起こされる接合およびプラスチックシールの亀裂の問題を解決するために、新しい二次リフロー溶接プロセスを開発および導入します。
2 はんだペースト印刷リフロー溶接キャビティと製造機構
2.1 溶接キャビティ
リフロー溶接後、製品を X 線で検査しました。図 1 に示すように、溶接部の色の薄い穴は、溶接層のはんだが不十分であることが原因であることがわかりました。
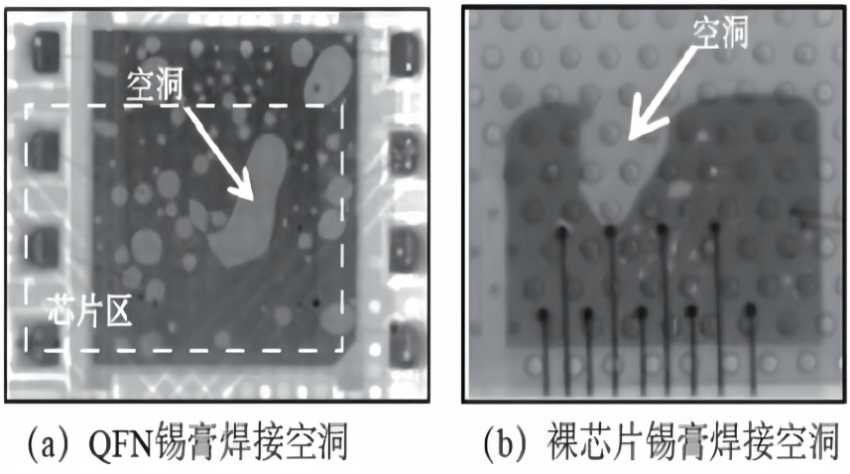
X線による気泡穴の検出
2.2 溶接キャビティの形成メカニズム
sAC305ソルダーペーストを例として、主な組成と機能を表1に示します。フラックスと錫ビーズはペースト状で結合しています。錫はんだとフラックスの重量比は約 9:1、体積比は約 1:1 です。
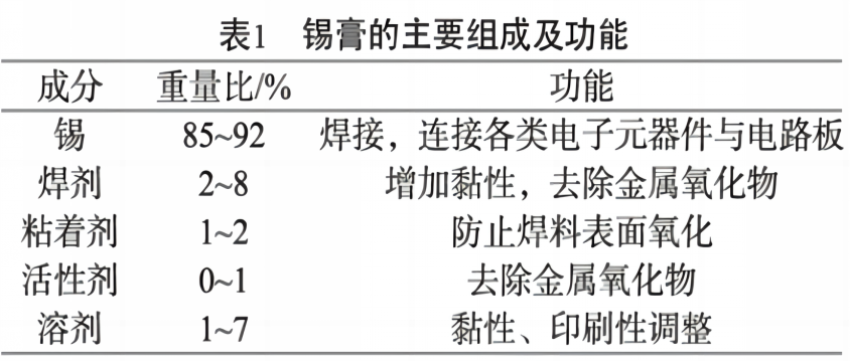
はんだペーストが印刷され、さまざまな電子部品が実装された後、はんだペーストは還流炉を通過するときに予熱、活性化、還流、冷却の 4 つの段階を経ます。図 2 に示すように、はんだペーストの状態も段階ごとに温度が異なると異なります。
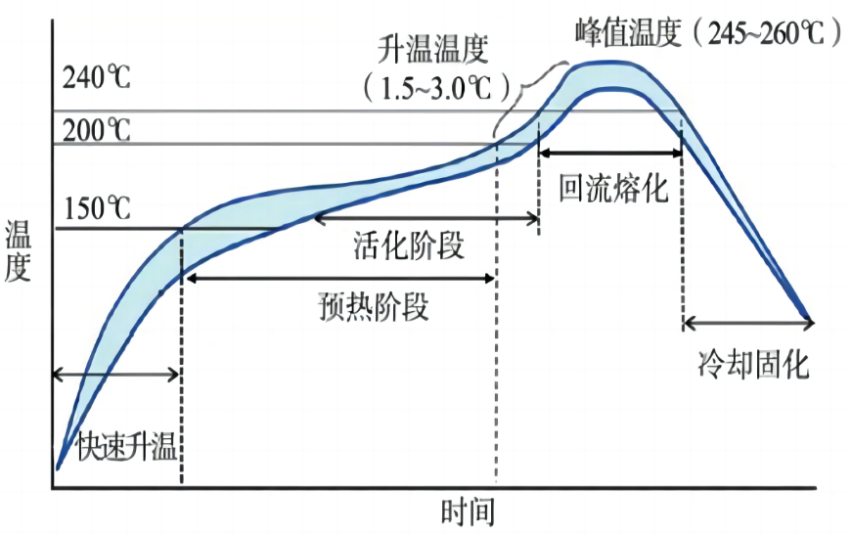
リフローはんだ付けの各エリアのプロファイル参考
予熱および活性化の段階では、加熱によりソルダペースト中のフラックスに含まれる揮発成分が揮発してガスになります。同時に溶接層表面の酸化物が除去される際にガスが発生します。これらのガスの一部は揮発してはんだペーストから残り、フラックスの揮発によりはんだビーズは緊密に凝縮します。還流段階では、はんだペースト内の残りのフラックスはすぐに蒸発し、錫ビーズが溶けます。少量のフラックス揮発性ガスと錫ビーズ間の空気の大部分は時間内に分散されず、はんだペースト内の残留物が分散されません。溶融錫と溶融錫の張力下ではハンバーガーサンドイッチ構造となっており、回路基板のはんだパッドや電子部品に引っかかり、液状錫に包まれたガスは上向きの浮力だけで抜けにくく、上部の溶解時間は非常に長い短い。溶けた錫が冷えて固体の錫になると、図3に示すように溶接層に気孔が現れ、はんだ穴が形成されます。
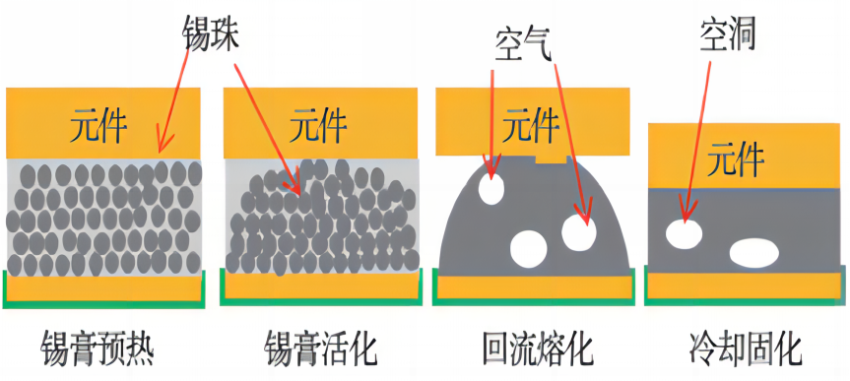
はんだペーストリフロー溶接により発生するボイドの模式図
溶接空洞の根本原因は、溶融後のはんだペースト中に包まれた空気や揮発性ガスが完全に排出されないことにあります。影響要因としては、はんだペーストの材質、はんだペーストの印刷形状、はんだペーストの印刷量、還流温度、還流時間、溶接サイズ、構造などが挙げられます。
3. リフロー溶接穴印刷はんだペーストの影響要因の検証
QFN およびベアチップ テストは、リフロー溶接ボイドの主な原因を確認し、はんだペーストによって印刷されるリフロー溶接ボイドを改善する方法を見つけるために使用されました。QFNおよびベアチップはんだペーストのリフロー溶接製品プロファイルを図4に示します。QFN溶接面のサイズは4.4mmx4.1mm、溶接面は錫めっき層(100%純錫)です。ベアチップの溶接サイズは3.0mm×2.3mm、溶接層はスパッタニッケルバナジウムバイメタル層、表面層はバナジウムです。基板の溶接パッドは無電解ニッケルパラジウム金メッキで、厚さは0.4μm/0.06μm/0.04μmでした。はんだペーストはSAC305を使用し、はんだペースト印刷装置はDEK Horizon APix、還流炉装置はBTUPyramax150N、X線装置はDAGExD7500VRを使用します。
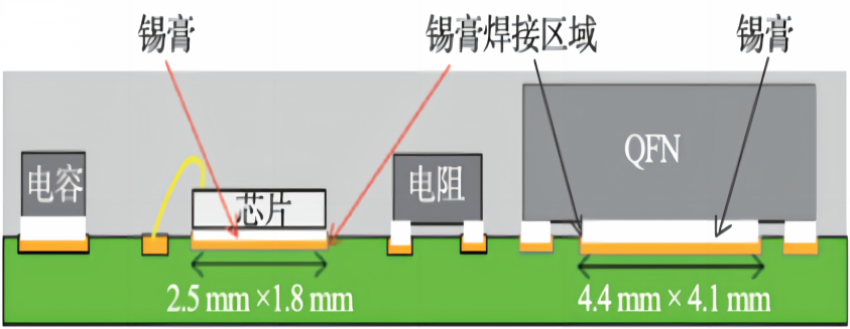
QFNおよびベアチップ溶接図
試験結果の比較を容易にするため、表2の条件でリフロー溶接を実施しました。
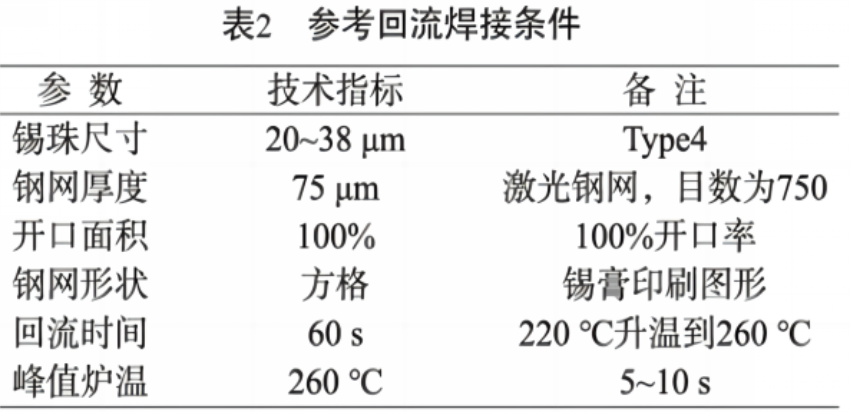
リフロー溶接条件表
表面実装およびリフロー溶接が完了した後、X線で溶接層を検出したところ、図5に示すように、QFNおよびベアチップの底部の溶接層に大きな穴が開いていることがわかりました。
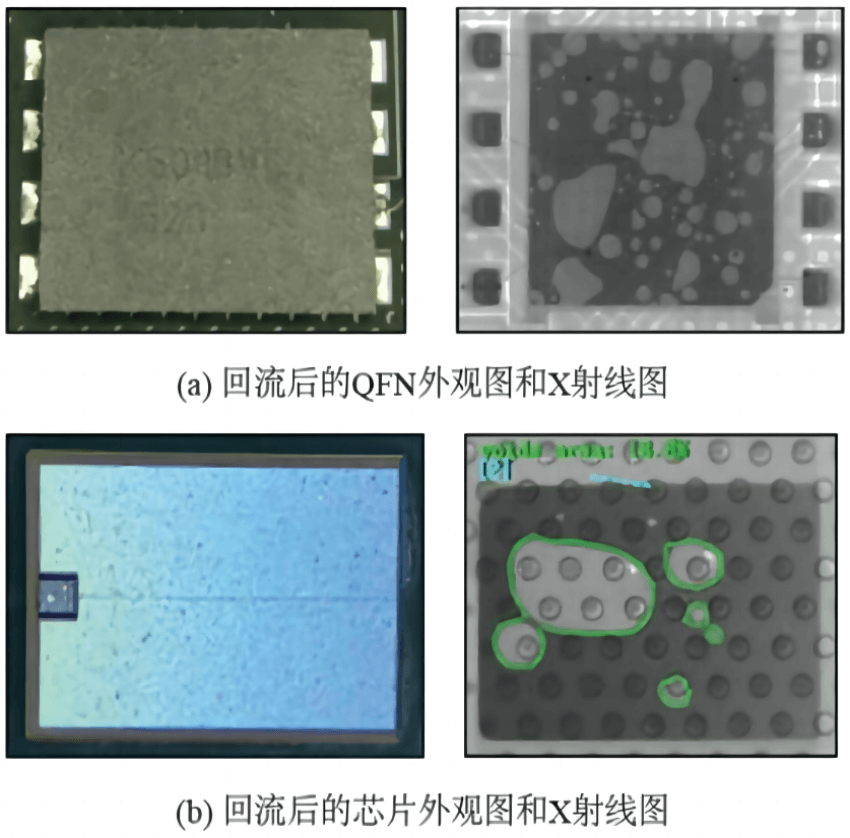
QFNとチップホログラム(X線)
錫ビードのサイズ、スチールメッシュの厚さ、開口面積率、スチールメッシュの形状、還流時間、および炉のピーク温度はすべてリフロー溶接ボイドに影響を与えるため、多くの影響要因があり、DOE テストによって直接検証され、実験の数も増加します。グループが大きすぎるでしょう。相関比較テストを通じて主な影響因子を迅速にスクリーニングして特定し、DOE を通じて主な影響因子をさらに最適化する必要があります。
3.1 はんだ穴およびはんだペースト錫ビーズの寸法
type3 (ビーズサイズ 25 ~ 45 μm) SAC305 はんだペーストのテストでは、他の条件は変わりません。リフロー後、はんだ層の穴が測定され、タイプ 4 のはんだペーストと比較されます。はんだ層の穴は 2 種類のはんだペースト間で大きな違いがないことがわかり、異なるビードサイズのはんだペーストははんだ層の穴に明らかな影響を与えておらず、影響因子ではないことを示しています。図1に示すように。6 図示の通り。
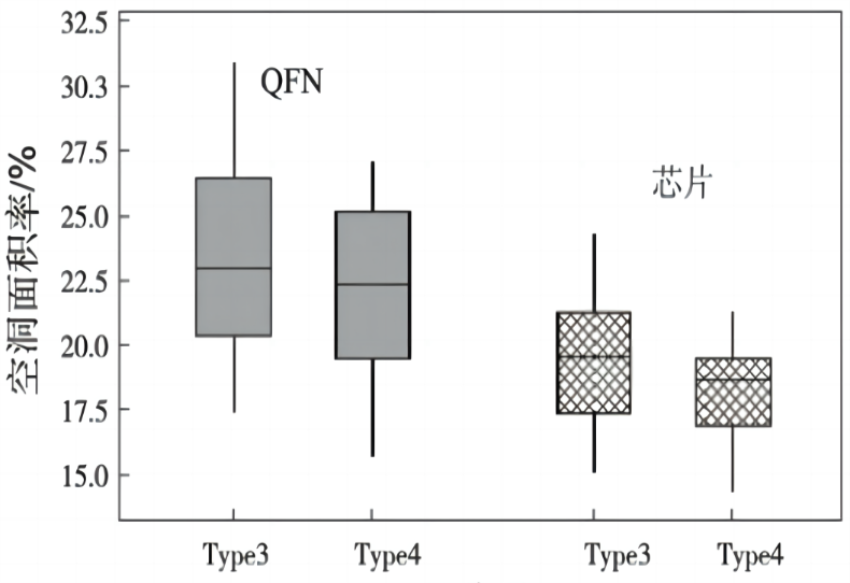
異なる粒子サイズの金属錫粉末の穴の比較
3.2 溶接キャビティと印刷鋼メッシュの厚さ
リフロー後、その他の条件を変えずに、厚さ50μm、100μm、125μmの印刷スチールメッシュを用いて溶接層のキャビティ面積を測定した。異なる厚さのスチールメッシュ (はんだペースト) が QFN に及ぼす影響を、厚さ 75 μm の印刷スチールメッシュの影響と比較したことがわかりました。スチールメッシュの厚さが増加するにつれて、キャビティ面積は徐々にゆっくりと減少します。図7に示すように、特定の厚さ(100μm)に達すると、キャビティ面積は反転し、スチールメッシュの厚さの増加に伴って増加し始めます。
これは、はんだペーストの量を増やすと、還流した液状錫がチップに覆われ、残留空気の逃げ口が四方のみ狭くなることを示しています。はんだペーストの量を変更すると、残留空気の逃げ口も増加し、液状錫に包まれた空気や揮発性ガスが逃げる液状錫の瞬間的な噴出により、液状錫が QFN やチップの周囲に飛散します。
試験の結果、スチールメッシュの厚さが増加すると、空気や揮発性ガスの流出による気泡の破裂も増加し、それに応じてQFNやチップの周囲に錫が飛散する確率も増加することがわかりました。
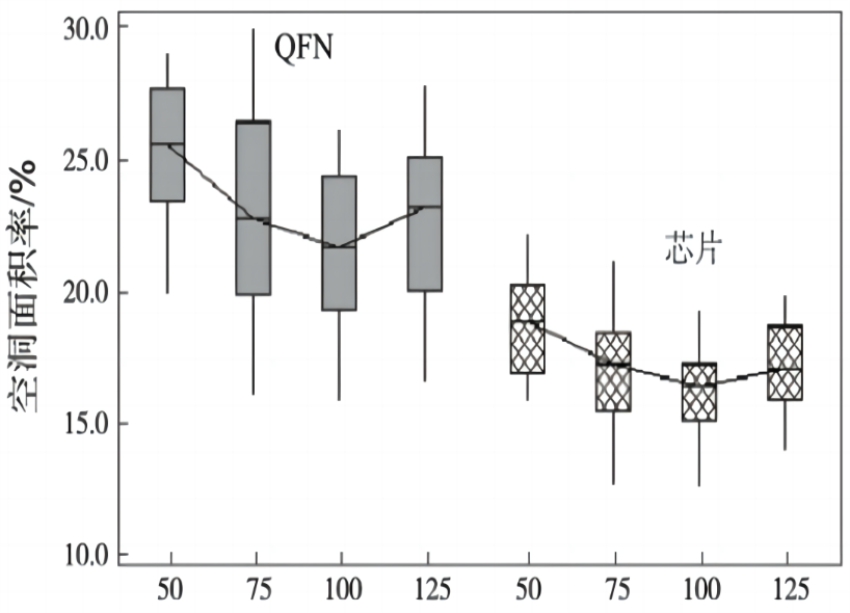
異なる厚さのスチールメッシュの穴の比較
3.3 溶接キャビティと鋼メッシュ開口部の面積比
開口率100%、90%、80%の印刷スチールメッシュをテストし、その他の条件は変更しませんでした。リフロー後、溶接層のキャビティ面積を測定し、開口率 100% で印刷したスチールメッシュと比較しました。図 8 に示すように、開口率 100% と 90% ~ 80% の条件では、溶接層の空隙に大きな差がないことがわかりました。
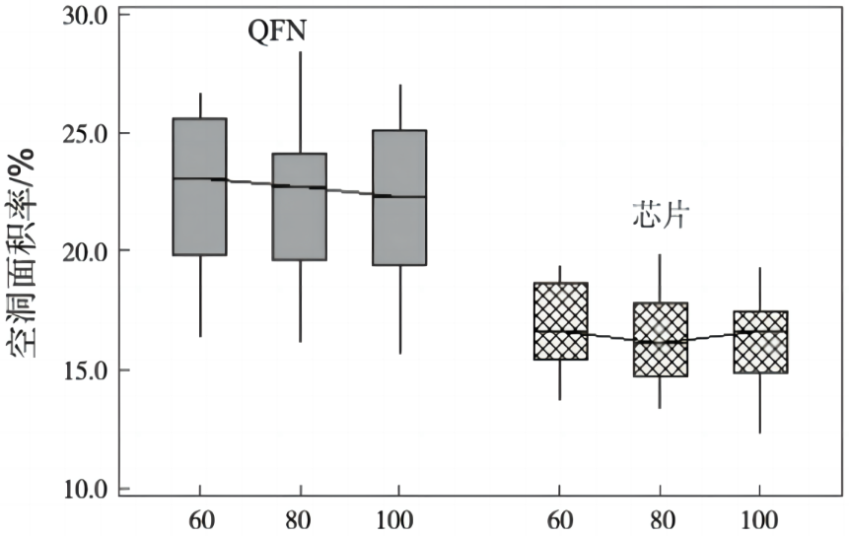
異なるスチールメッシュの異なる開口面積のキャビティの比較
3.4 溶接キャビティと印刷されたスチールメッシュの形状
ストリップbと傾斜グリッドcのはんだペーストの印刷形状テストでは、他の条件は変わりません。リフロー後、溶接層のキャビティ面積を測定し、グリッドaの印刷形状と比較します。図9に示すように、グリッド、ストリップ、傾斜グリッドの条件下では、溶接層のキャビティに大きな違いがないことがわかります。
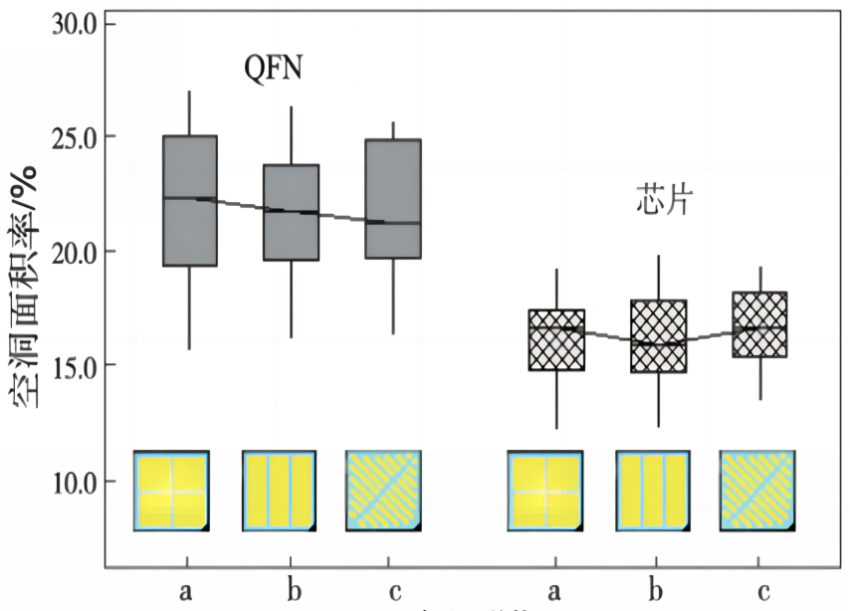
スチールメッシュの異なる開口モードでの穴の比較
3.5 溶接キャビティと還流時間
長時間還流時間(70秒、80秒、90秒)試験後、他の条件は変化させず、還流後に溶接層の穴を測定し、還流時間60秒と比較して、溶接層の穴が増加することがわかりました。図 10 に示すように、還流時間を長くすると溶接穴の面積は減少しましたが、減少幅は時間の経過とともに徐々に減少しました。これは、還流時間が不十分な場合、還流時間を長くすると空気が完全にオーバーフローするのに役立つことを示しています。液体錫に包まれた空気は、溶融した液体錫に包まれていますが、還流時間が一定時間以上長くなると、液体錫に包まれた空気は再び溢れにくくなります。還流時間は溶接キャビティに影響を与える要因の 1 つです。
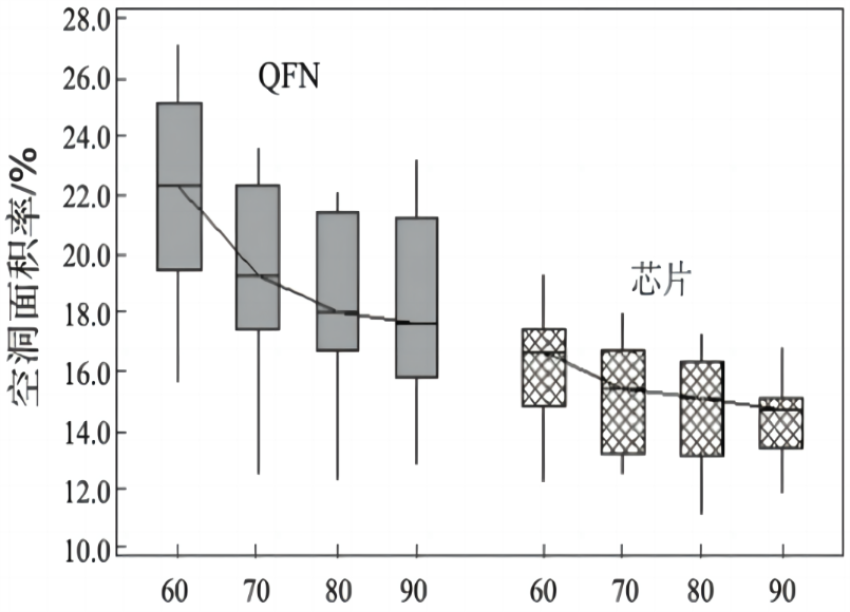
異なる還流時間の長さのボイド比較
3.6 溶接キャビティと炉のピーク温度
240℃と250℃のピーク炉温度試験およびその他の条件を変えずに、リフロー後の溶接層のキャビティ面積を測定し、260℃のピーク炉温度と比較すると、異なるピーク炉温度条件では、キャビティの溶接層のキャビティ面積が減少することがわかりました。図 11 に示すように、QFN とチップの溶接層は大きく変化しませんでした。これは、炉のピーク温度の違いが QFN とチップの溶接層の穴に明白な影響を与えず、影響要因ではないことを示しています。
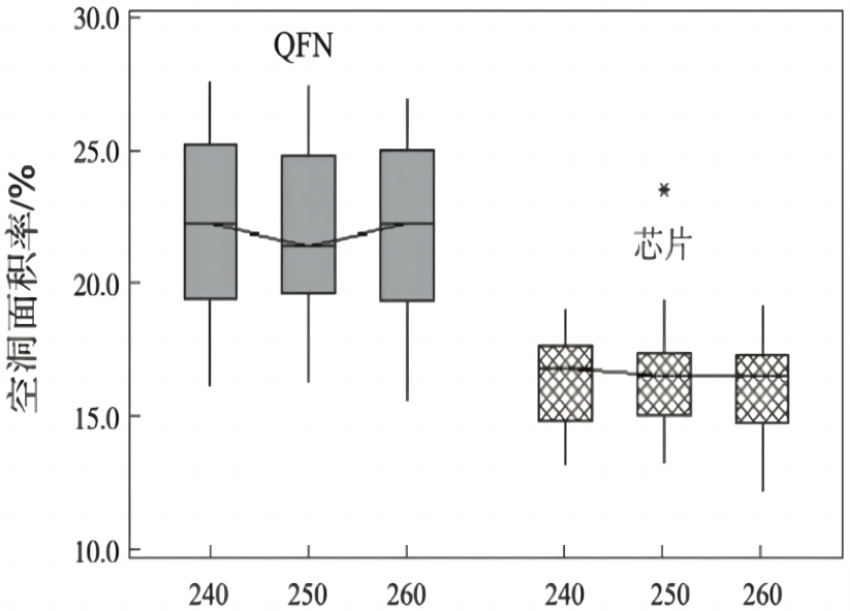
異なるピーク温度の比較を無効にする
上記のテストは、QFN とチップの溶接層キャビティに影響を与える重要な要因は、還流時間とスチール メッシュの厚さであることを示しています。
4 はんだペースト印刷リフロー溶接キャビティ改善
4.1溶接キャビティを改善するためのDOEテスト
QFNとチップの溶接層の穴は、主な影響因子(還流時間とスチールメッシュの厚さ)の最適値を見つけることによって改善されました。はんだペーストはSAC305 type4、スチールメッシュ形状は格子型(開度100%)、炉ピーク温度は260℃、その他の試験条件は試験装置と同様とした。DOE 試験と結果を表 3 に示します。QFN およびチップ溶接穴に対するスチールメッシュの厚さと還流時間の影響を図 12 に示します。主な影響因子の相互作用解析により、100 μm のスチールメッシュ厚さを使用すると、 80 秒の還流時間により、QFN とチップの溶接キャビティを大幅に減らすことができます。QFNの溶接巣率は最大27.8%から16.1%に、チップの溶接巣率は最大20.5%から14.5%に減少しました。
試験では、最適条件(スチールメッシュ厚さ100μm、還流時間80秒)で1000個の製品を製造し、100個のQFNとチップの溶接空洞率をランダムに測定しました。QFNの平均溶接巣率は16.4%、チップの平均溶接巣率は14.7%であった。チップとチップの溶接巣率は明らかに減少している。
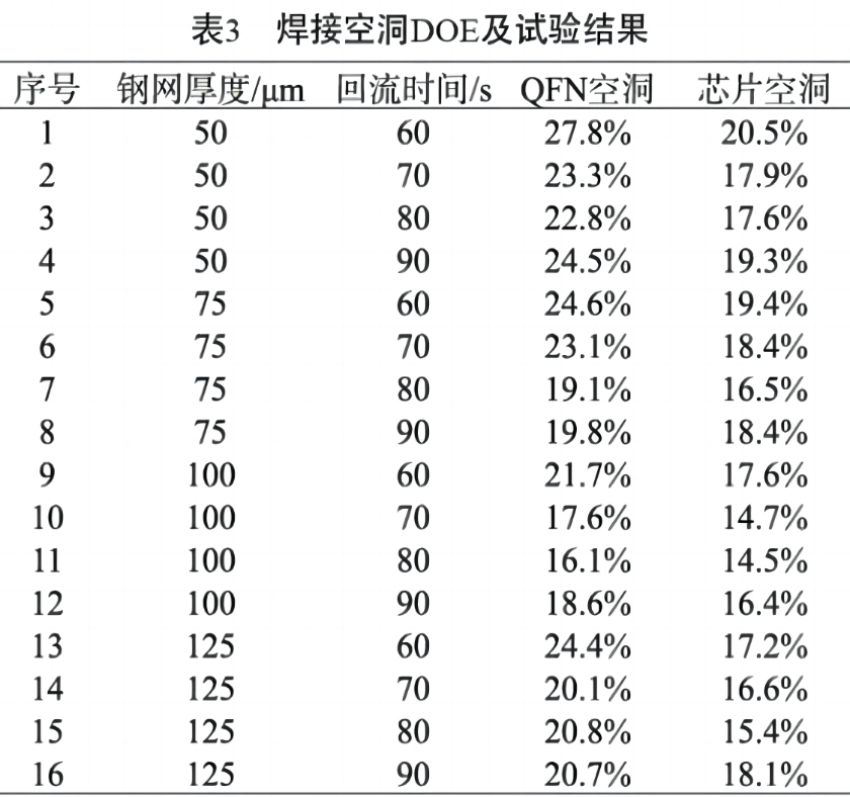
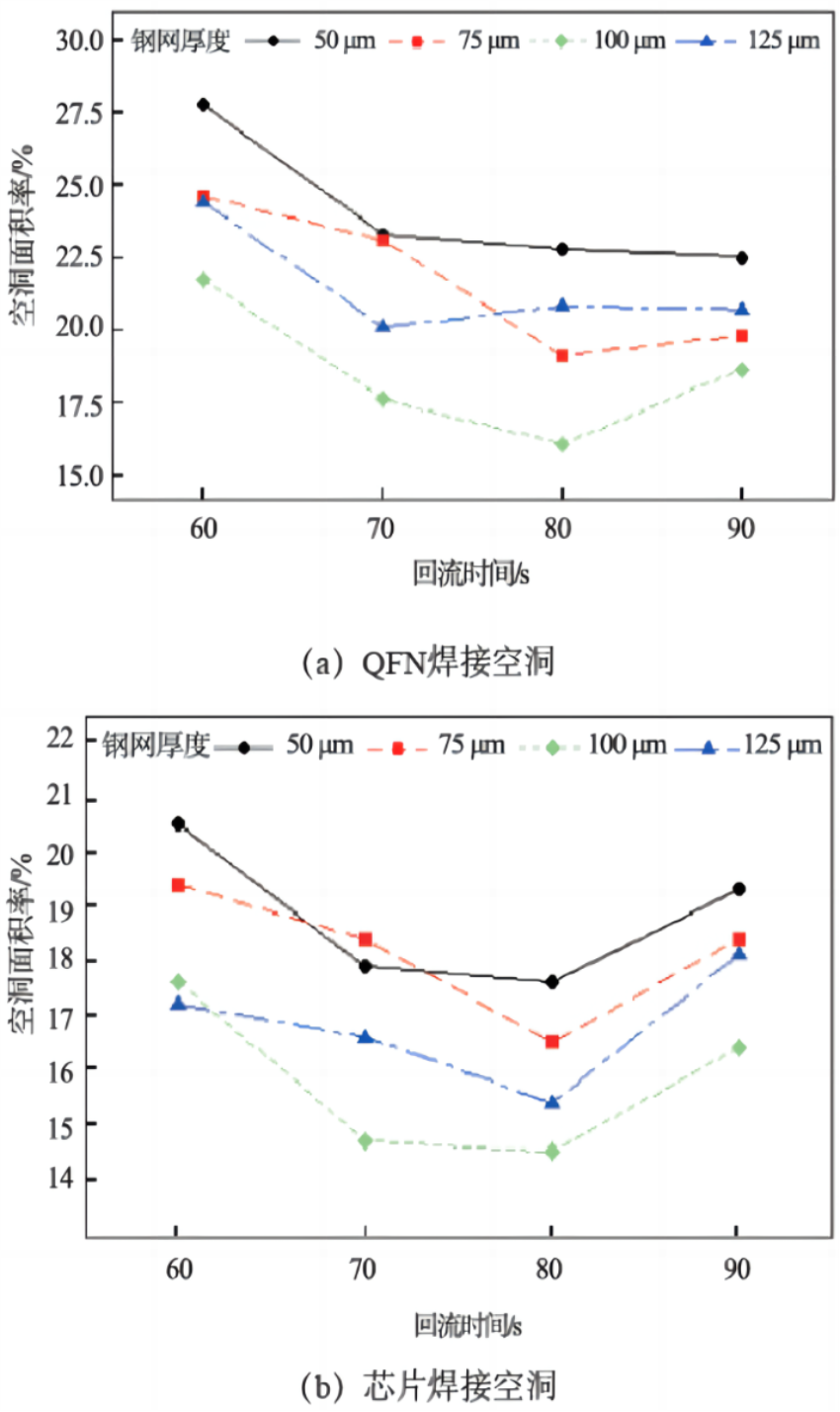
4.2 新プロセスによる溶接キャビティの改善
実際の生産状況と試験により、チップ底部の溶接キャビティ面積が10%未満の場合、リードボンディングおよびモールド時にチップキャビティ位置の亀裂問題が発生しないことがわかります。DOEによって最適化されたプロセスパラメータは、従来のはんだペーストリフロー溶接における穴の解析と解決の要件を満たすことができず、チップの溶接キャビティ面積率をさらに削減する必要があります。
チップははんだ上に覆われているため、はんだ中のガスが逃げるのを妨げるため、はんだ被覆ガスを除去または低減することにより、チップ底部の穴あき率がさらに低下する。1回のはんだペースト印刷、1回のはんだペースト印刷、QFNとベアチップを覆わずにはんだ内のガスを排出するリフローの2回のリフロー溶接という新プロセスを採用。二次はんだペースト印刷、パッチ、二次還流の具体的なプロセスを図 13 に示します。
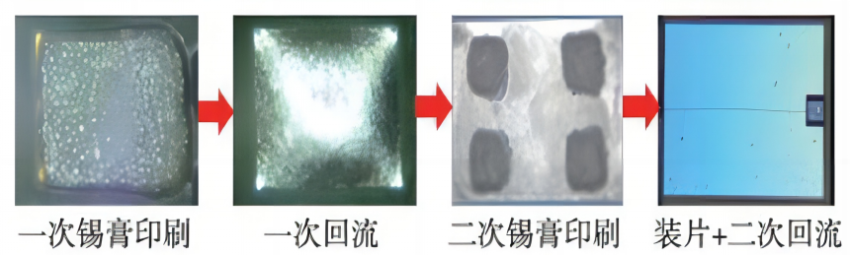
75μmの厚さのはんだペーストを初めて印刷すると、チップカバーのないはんだ中のガスのほとんどが表面から抜け出し、還流後の厚さは約50μmになります。一次還流の完了後、冷却されて固化したはんだの表面に小さな正方形が印刷されます(はんだペーストの量を減らし、ガスの流出量を減らし、はんだのスパッタを減らすか排除するため)。厚さ 50 μm (上記のテスト結果では 100 μm が最適であることが示されているため、二次印刷の厚さは 100 μm.50 μm = 50 μm)、チップを取り付け、80 秒で戻ります。図 14 に示すように、1 回目の印刷とリフロー後のはんだには穴はほとんどなく、2 回目の印刷でははんだペーストが小さく、溶接穴も小さくなっています。
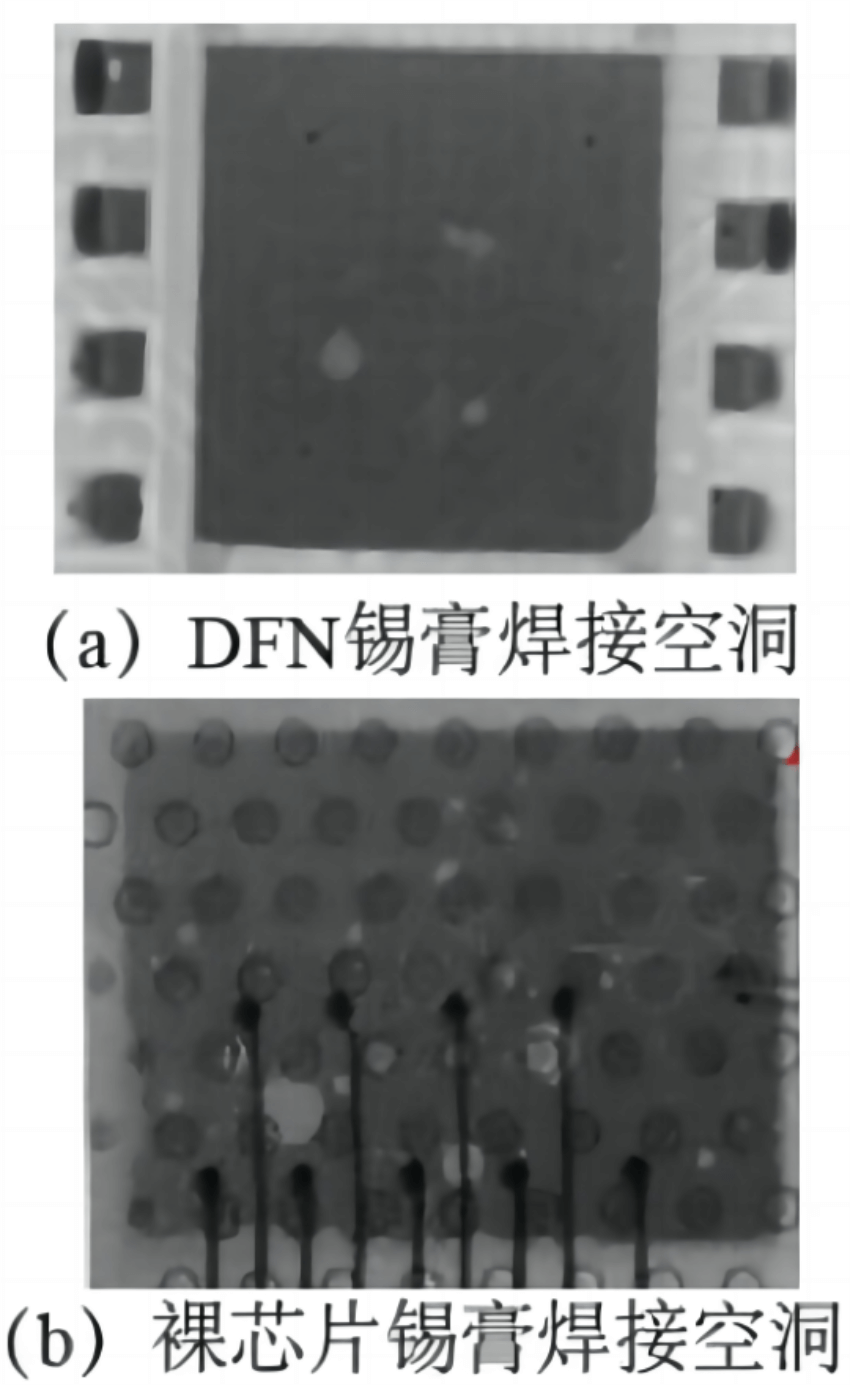
はんだペースト2回印刷後、中空絞り加工
4.3 溶接キャビティ効果の検証
2000個の製品を生産(第1印刷スチールメッシュの厚さは75μm、第2印刷スチールメッシュの厚さは50μm)、その他の条件は変更せず、500個のQFNとチップ溶接キャビティ率をランダムに測定したところ、新しいプロセスが最適であることがわかりました。 1 回目の還流後は空洞なし、2 回目の還流後 QFN 最大溶接巣率は 4.8%、チップの最大溶接巣率は 4.1% です。図 15 に示すように、元の単一ペースト印刷溶接プロセスと DOE 最適化プロセスと比較して、溶接キャビティが大幅に減少しました。すべての製品の機能テスト後、チップ クラックは見つかりませんでした。
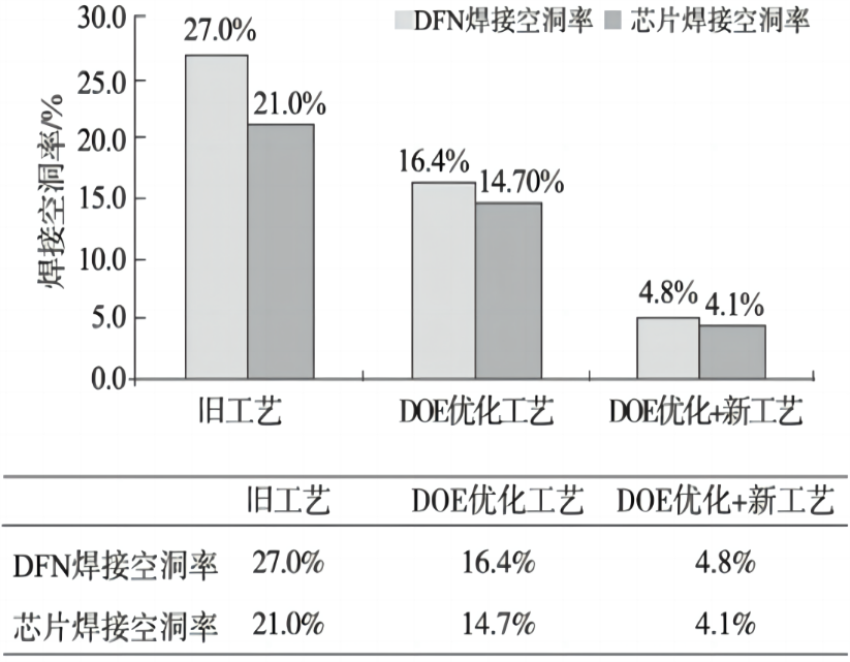
5 まとめ
はんだペーストの印刷量や還流時間の最適化により溶接巣面積は減少するものの、依然として溶接巣率は大きい。2 つのはんだペースト印刷リフロー溶接技術を使用すると、溶接キャビティ率を効果的かつ最大化できます。QFN回路ベアチップの量産時の溶接面積はそれぞれ4.4mm×4.1mm、3.0mm×2.3mmです。リフロー溶接の空洞率は5%以下に制御されており、リフロー溶接の品質と信頼性が向上します。この論文の研究は、大面積溶接面の溶接キャビティ問題を改善するための重要な参考資料を提供します。