高精度 PCBA 回路基板 DIP プラグイン選択ウェーブはんだ溶接設計は要件に従う必要があります。
従来の電子組立プロセスでは、通常、ウェーブ溶接技術が、穴あきインサート要素 (PTH) を備えたプリント基板コンポーネントの溶接に使用されます。
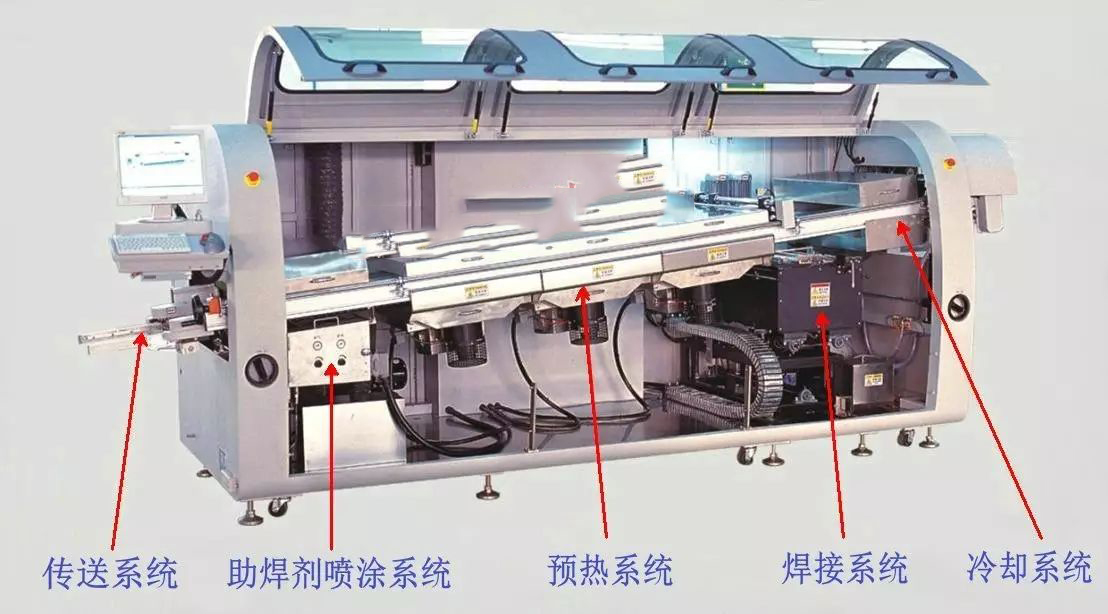
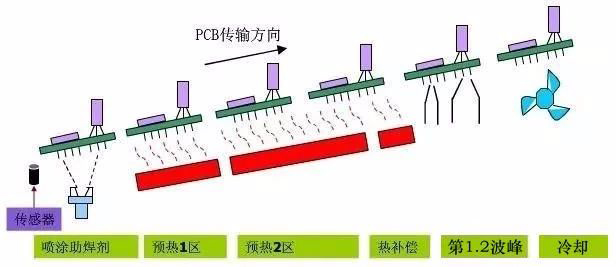
DIP ウェーブはんだ付けには多くの欠点があります。
1. 高密度、ファインピッチの SMD 部品を溶接面に分布させることができません。
2. はんだのブリッジ抜けやはんだ抜けが多い。
3.フラックスをスプレーする必要があります。大きな熱衝撃によりプリント基板が反ったり、変形したりすることがあります。
現在の回路アセンブリの密度はますます高くなっており、高密度でファインピッチの SMD 部品がはんだ付け面に分布することは避けられません。従来のウェーブはんだ付けプロセスでは、これを行うことはできませんでした。一般に、はんだ付け面上の SMD コンポーネントは個別にリフローはんだ付けのみ可能です。、その後、残りのプラグインはんだ接合部を手動で修復しますが、はんだ接合部の品質の一貫性が低いという問題があります。
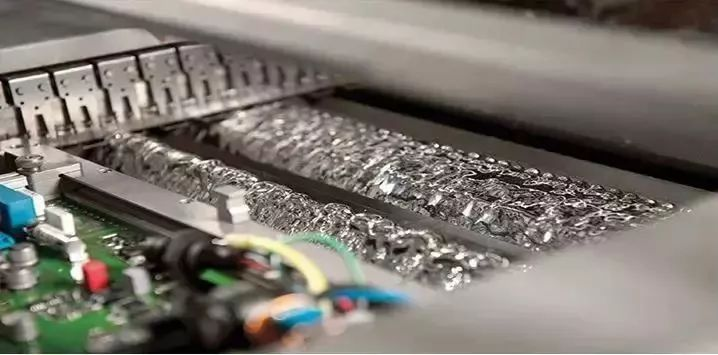
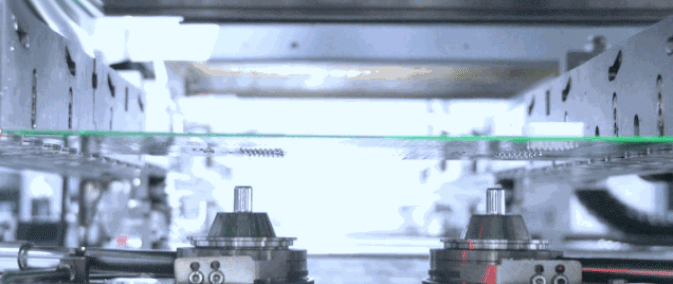
スルーホール部品(特に大容量部品やファインピッチ部品)のはんだ付けはますます困難になり、特に鉛フリーや高信頼性が要求される製品では、手はんだ付けのはんだ付け品質では高品質を満たすことができなくなりました。電気設備。生産要件に応じて、ウェーブはんだ付けは、特定の用途における小ロットおよび多品種の生産および応用に完全には対応できません。選択的ウェーブはんだ付けの応用は、近年急速に発展しました。
THT 穿孔コンポーネントのみを備えた PCBA 回路基板の場合、現時点でもウェーブはんだ付け技術が最も効果的な処理方法であるため、ウェーブはんだ付けを選択的はんだ付けに置き換える必要はありません。これは非常に重要です。ただし、混合テクノロジ基板には選択的はんだ付けが不可欠であり、使用するノズルの種類に応じて、ウェーブはんだ付け技術を洗練された方法で再現できます。
部分はんだ付けには、ドラッグはんだ付けとディップはんだ付けの 2 つの異なるプロセスがあります。
選択的引きはんだ付けプロセスは、単一の小さな先端はんだウェーブで実行されます。引きはんだ付けプロセスは、PCB 上の非常に狭いスペースのはんだ付けに適しています。例: 個々のはんだ接合部またはピン、単一列のピンをドラッグしてはんだ付けできます。
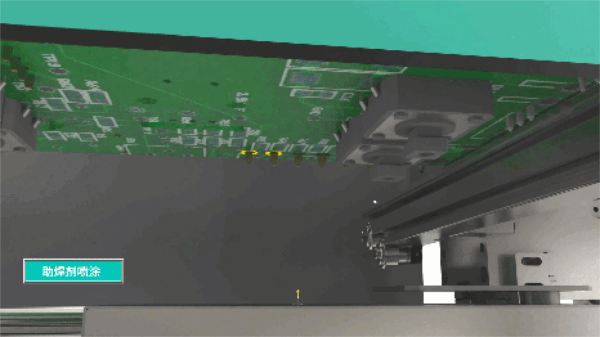
選択的ウェーブはんだ付け技術は、SMT 技術で新しく開発された技術であり、その外観は、高密度で多様な混合 PCB 基板の組み立て要件をほぼ満たしています。選択的ウェーブはんだ付けには、はんだ接合パラメータを独立して設定できる、PCB への熱衝撃が少ない、フラックスのスプレーが少ない、はんだ付けの信頼性が高いという利点があります。複雑な PCB には、徐々に不可欠なはんだ付け技術になりつつあります。
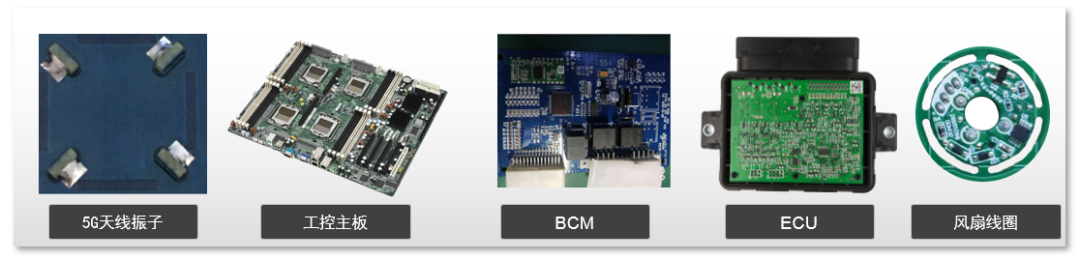
周知のとおり、PCBA 回路基板の設計段階で製品の製造コストの 80% が決まります。同様に、多くの品質特性は設計時に固定されます。したがって、PCB 回路基板の設計プロセスでは、製造要素を十分に考慮することが非常に重要です。
優れた DFM は、PCBA 実装部品メーカーにとって、製造欠陥の削減、製造プロセスの簡素化、製造サイクルの短縮、製造コストの削減、品質管理の最適化、製品市場の競争力の強化、製品の信頼性と耐久性の向上を実現する重要な方法です。これにより、企業は最小限の投資で最大の利益を得ることができ、半分の労力で 2 倍の成果を達成することができます。
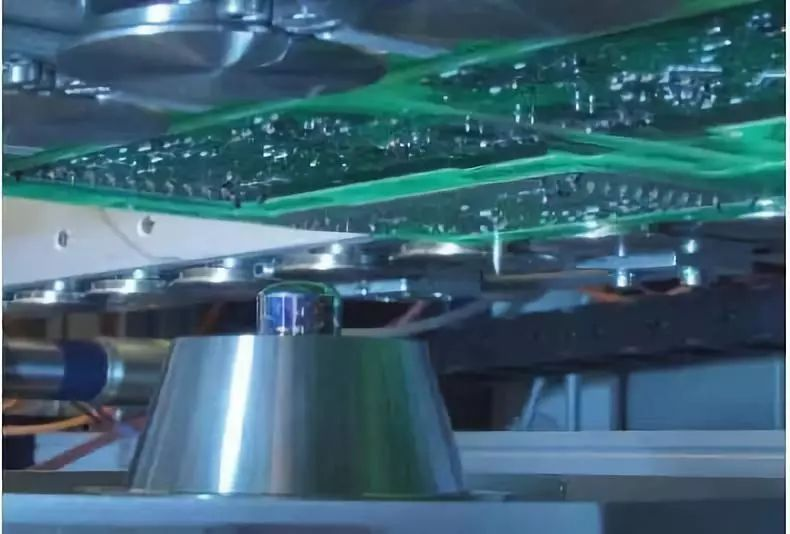
今日に至るまでの表面実装部品の開発では、SMT エンジニアは回路基板設計技術に習熟しているだけでなく、SMT 技術に対する深い理解と豊富な実務経験も求められています。はんだペーストやはんだの流れ特性を理解していない設計者は、ブリッジング、チッピング、ツームストーン、ウィッキングなどの理由や原理を理解することが困難であることが多く、合理的にパッドパターンを設計することに苦労することが困難だからです。設計の製造性、テスト容易性、コストや経費削減の観点から、さまざまな設計上の問題に対処することは困難です。完璧に設計されたソリューションであっても、DFM と DFT (検出可能性の設計) が不十分な場合、製造コストとテストコストが多額にかかります。